Auckland International Airport, New Zealand.
Auckland International Airport
SIZE
~4300 m²
FABRIC
Flexlight 702 s2
AWARDS
2022 OFPANZ Structures over 100m² Winner
BUILD
The goal of this project was to create an exceptional pedestrian experience by constructing a covered walkway connecting the airport terminal to the parking area located north of Ray Emery Drive. This was necessary due to the closure of the main car park for the development of a new multi-story facility. The walkway also needed to provide a smooth transition to the rental vehicle pick-up and drop-off areas, enhancing the convenience for travelers.
What made this project particularly complex was the vast network of essential services running underground at the airport, which could not be moved. These services are critical to the airport's operations, requiring the design and engineering to work around or over them. This necessitated extensive collaboration with Beca (Civil Designers) and Fulton Hogan (Civil Contractors). The project’s tight timeline meant that both the steel and PVC components had to be fabricated directly from 3D models, leaving no room for error.
The coordination between various trades—such as wayfinding, lighting, and communications—added to the complexity. With up to 20 stakeholders involved in multiple meetings each week, the level of communication and collaboration needed to be seamless. Two third-party engineering companies were brought in to handle the constant adjustments required throughout the project.
Despite these challenges, the result exceeded the client’s expectations by delivering an aesthetically pleasing, functional walkway that effectively connects the terminal to the northern car parks. It also provides a seamless flow for customers accessing rental vehicles. Notably, the project was completed over the course of two lockdowns. The original contract was terminated in March 2020 due to the first lockdown, but the project was re-contracted, and stage one was successfully completed in January 2021, despite enduring another lockdown. This required extensive coordination and trust between the project team and AIA, helping to build a strong relationship that has resulted in ongoing business.
From an engineering standpoint, navigating the extensive underground services was a significant challenge. Working closely with Beca, the team confirmed the most feasible column set-out, which then informed the engineering design. This task alone was monumental, as the project involved 300 meters of fabric structures. The foundation engineer developed five different foundation options, allowing Fulton Hogan flexibility on site when encountering unexpected obstacles. On several occasions, adjustments had to be made as services were found in unforeseen locations.
From a management perspective, the scale and speed of the project added layers of complexity. To meet the original pre-COVID timeline, some of the PVC panels were fabricated in the Philippines, adding further logistical challenges. Following the termination of the first contract, the original AIA team was replaced, requiring the project team to onboard and educate a new group about the decisions made previously, further complicating the process.
In the end, this project was both vast in scope and intricate in execution. It required years of stakeholder engagement, from the initial column layout to the engineering of four non-uniform structures, five foundation options, and the management of multiple stakeholders and trades. What started as a fast-paced project took 2.5 years to complete, and the result is a testament to the resilience and dedication of the entire team.
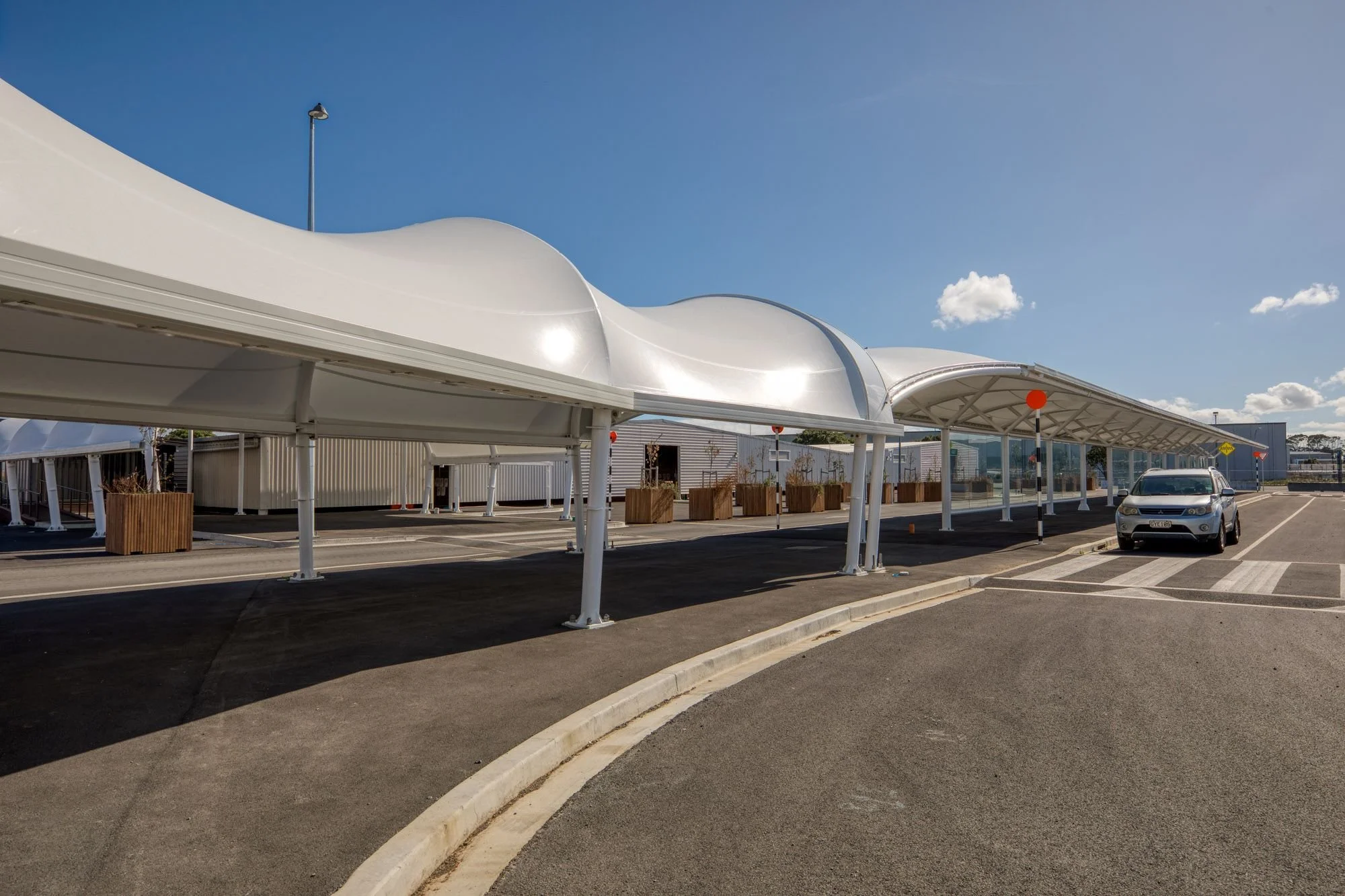
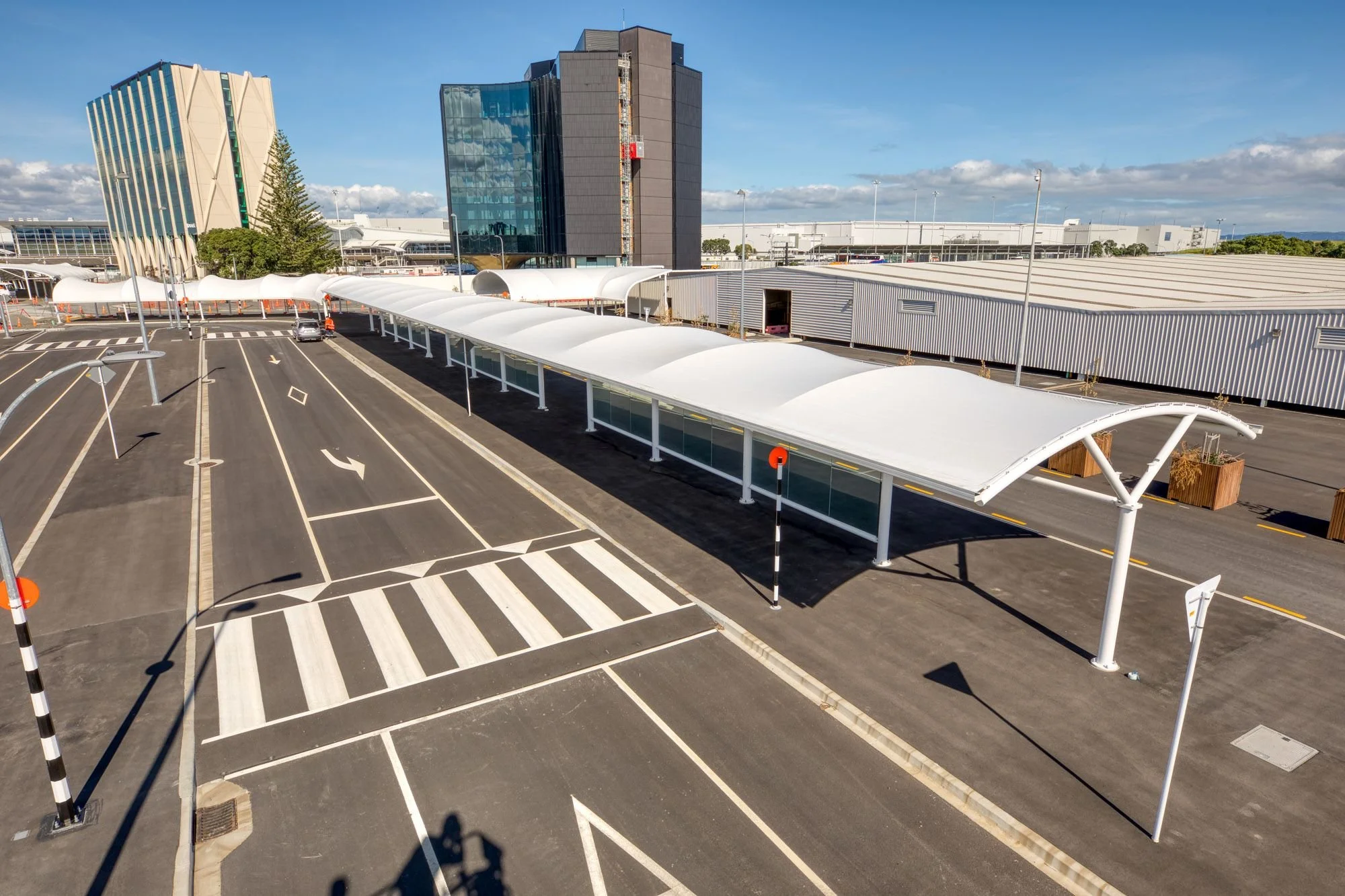
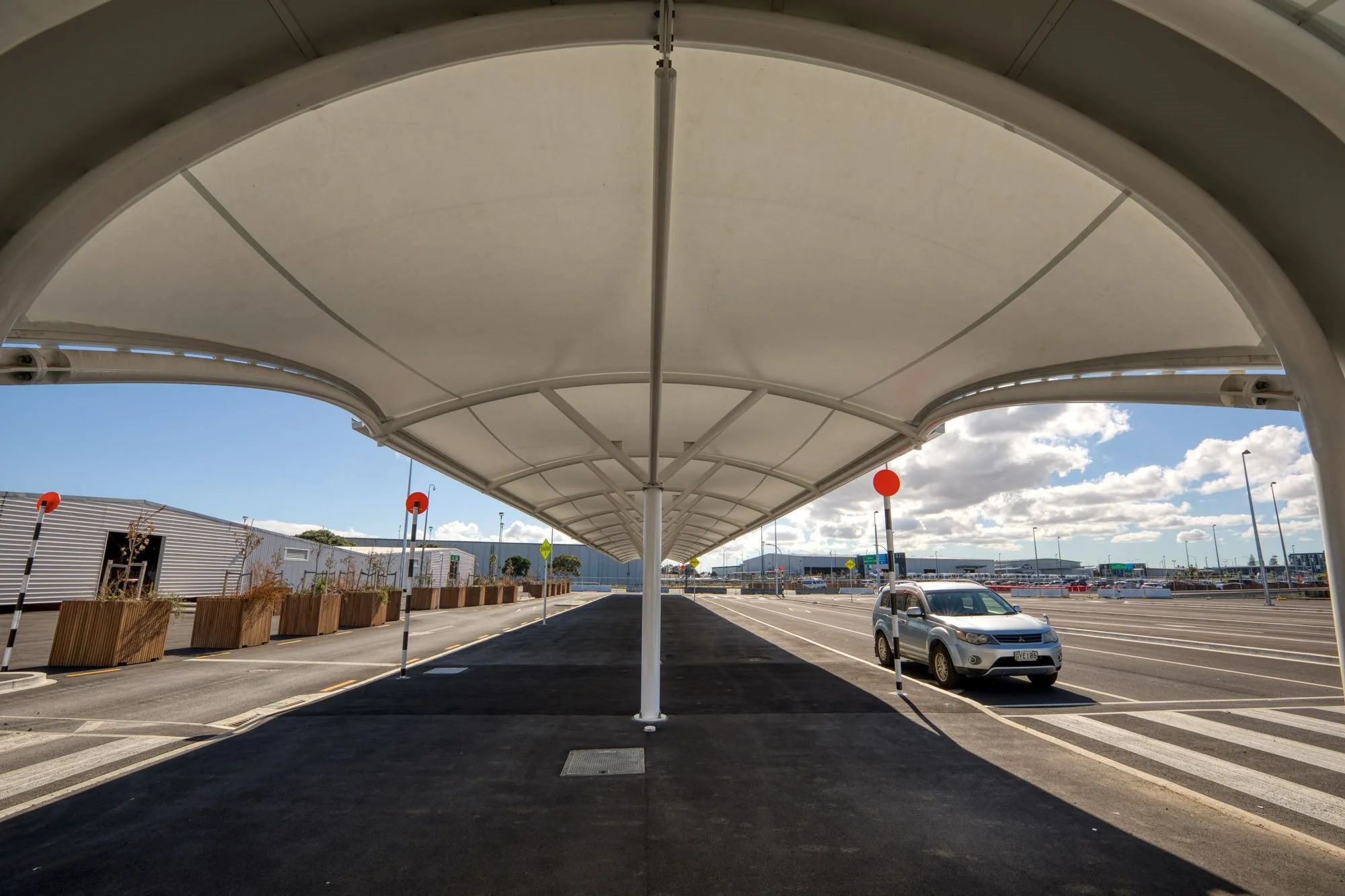



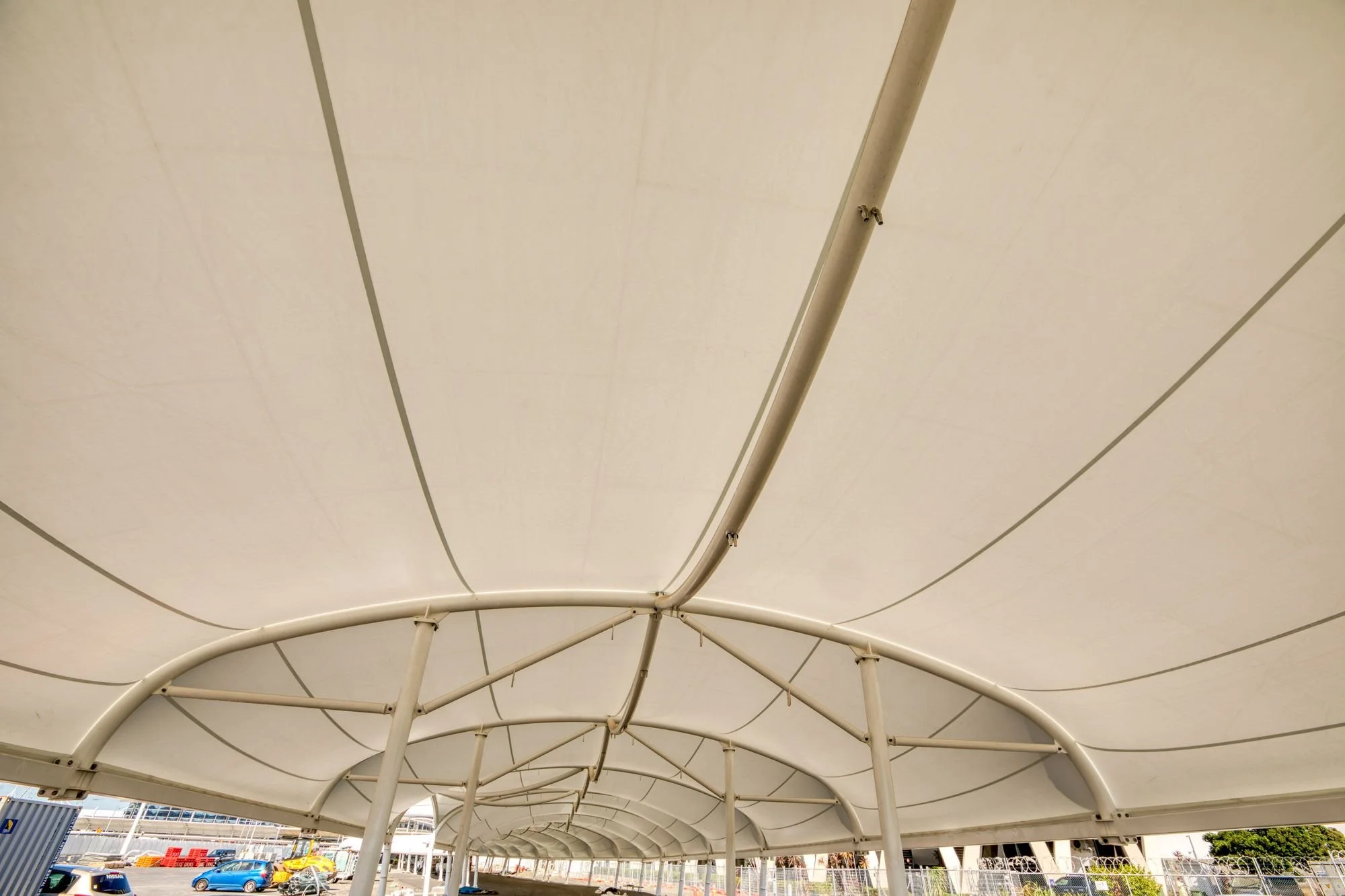



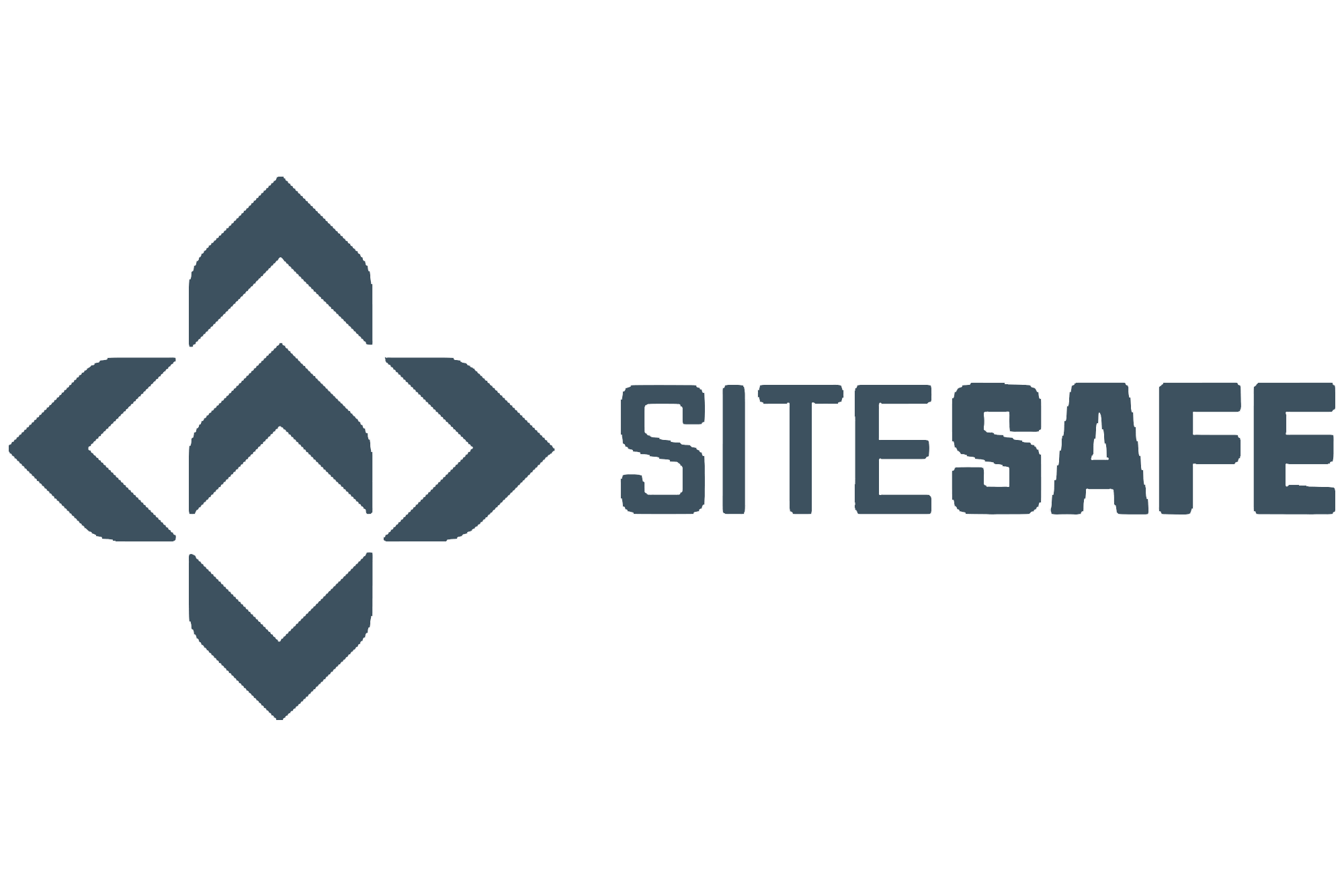
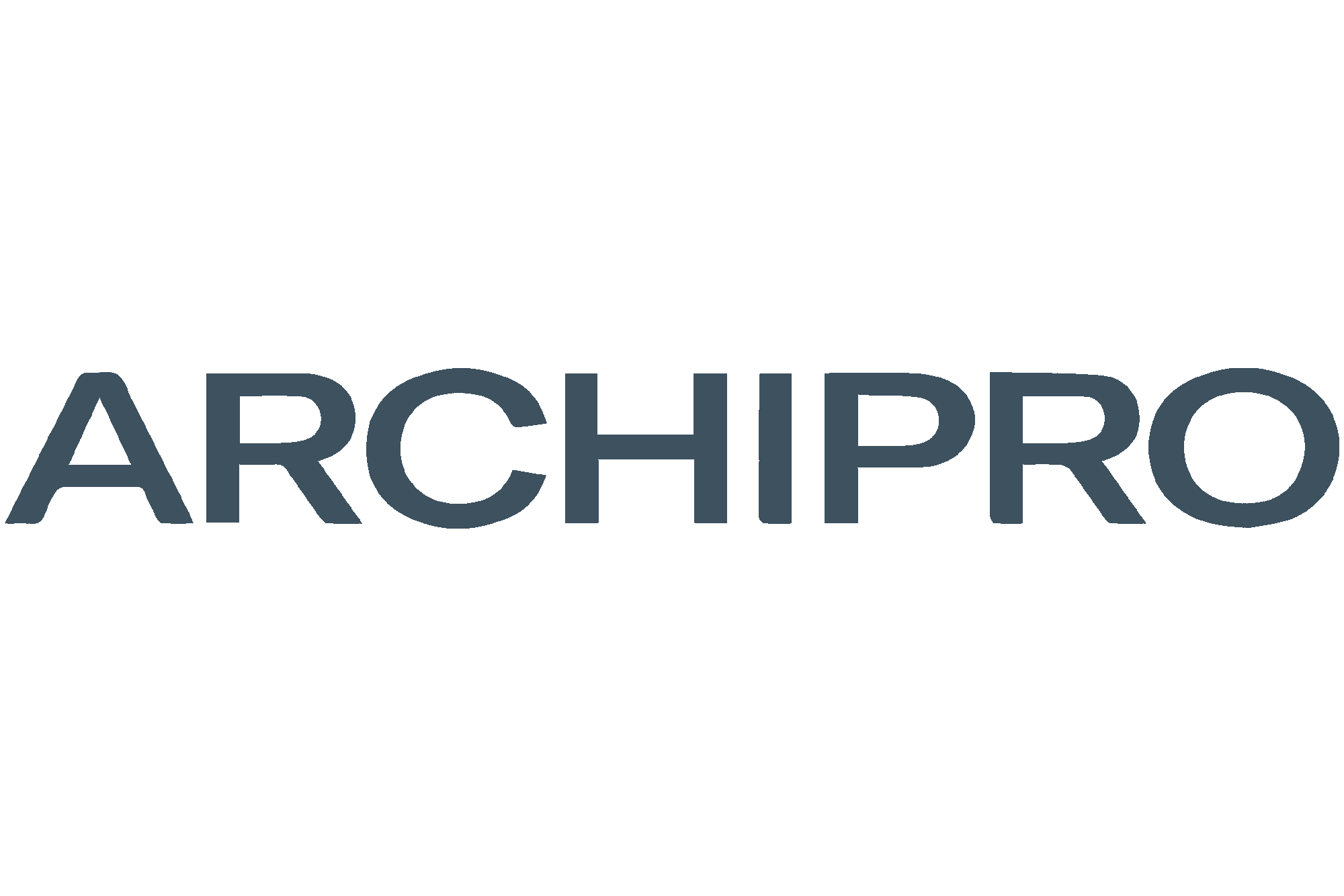




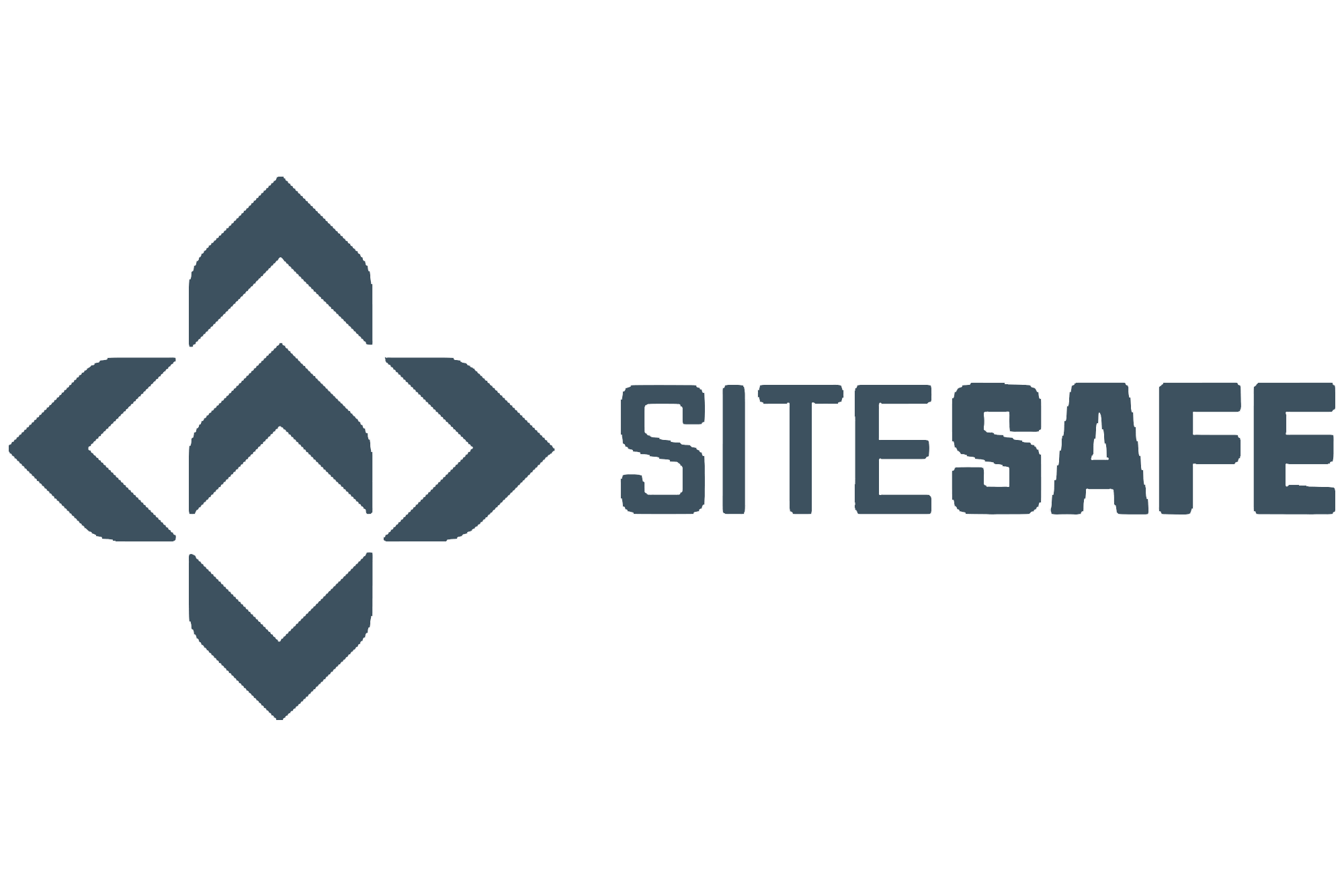
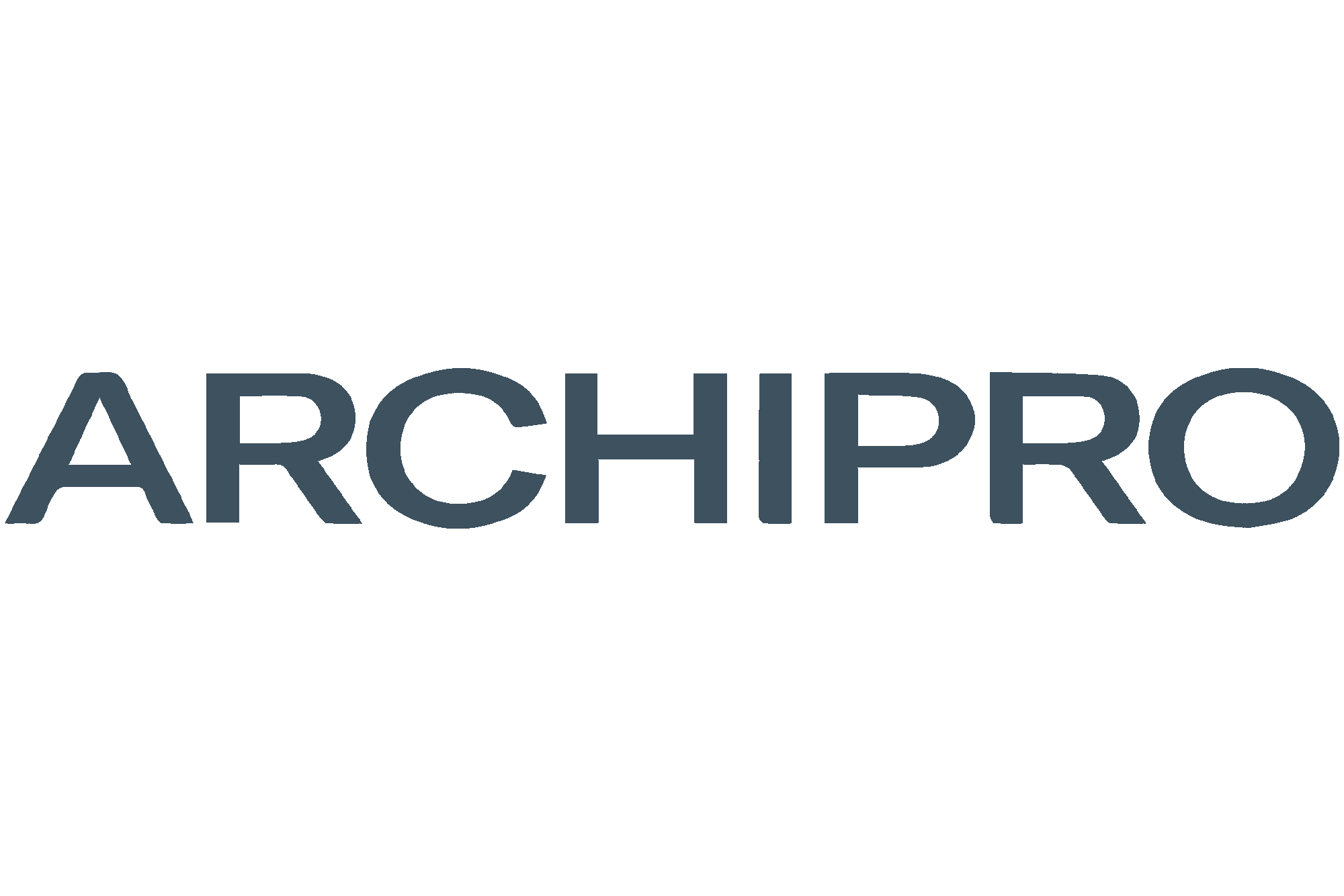




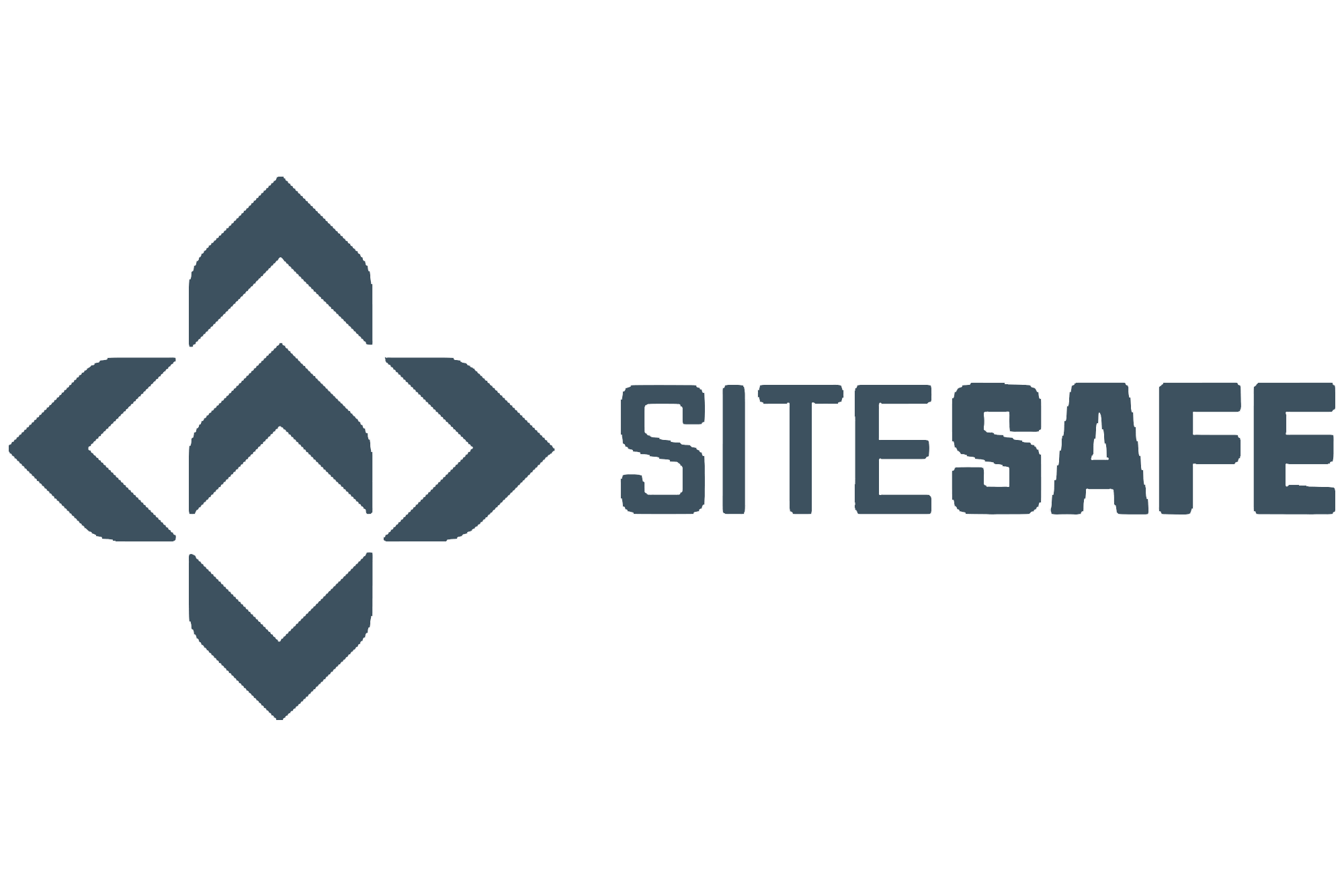
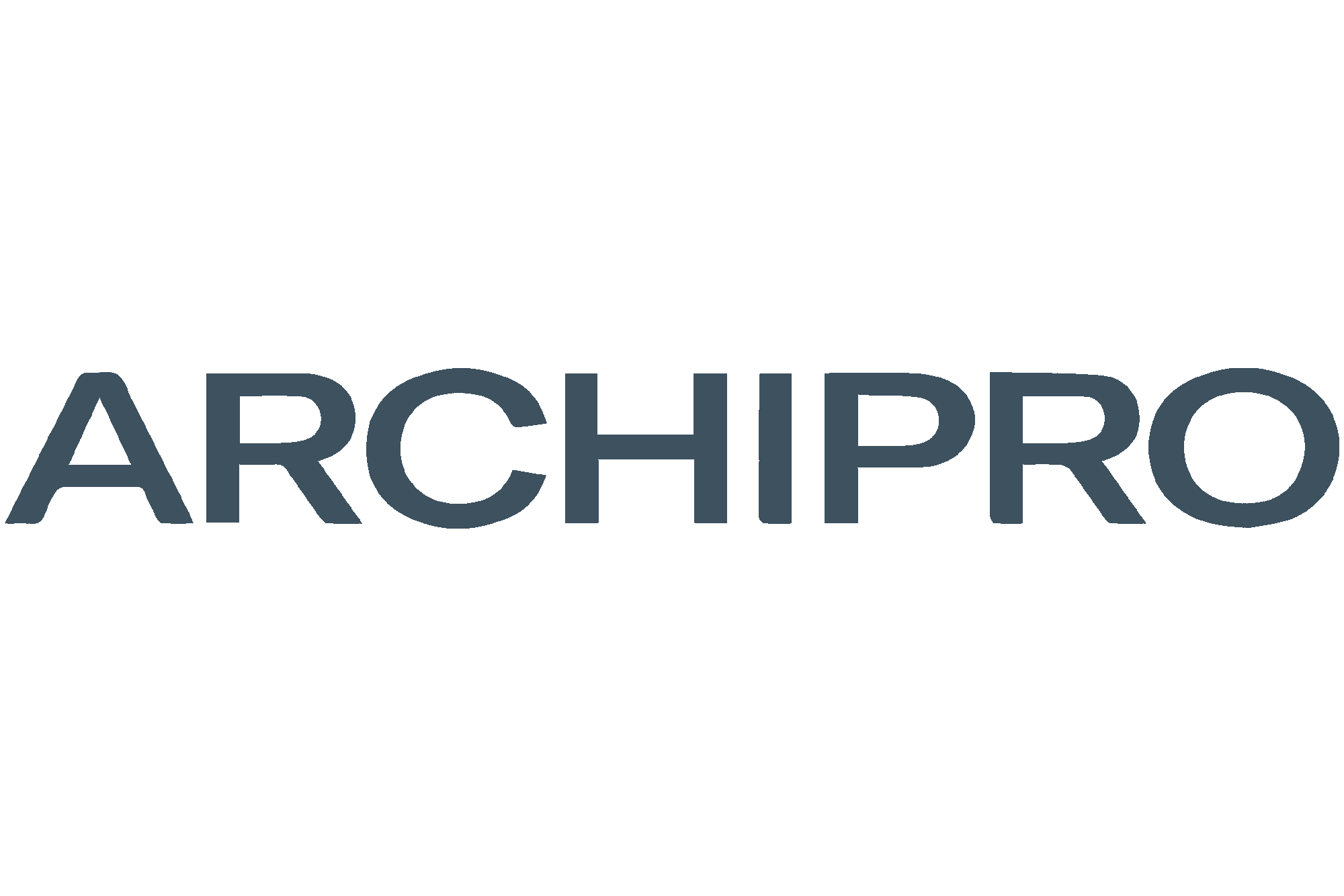

